Огнеупорные бетоны с низким содержанием цемента сравнивают с традиционными огнеупорными бетонами на основе алюминатного цемента. Количество добавляемого цемента в традиционные огнеупорные бетоны на основе алюминатного цемента обычно составляет 12–20%, а количество добавляемой воды — 9–13%. Из-за большого количества добавляемой воды тело отливки имеет много пор, неплотное и имеет низкую прочность; из-за большого количества добавляемого цемента, хотя и можно получить более высокую нормальную и низкотемпературную прочность, прочность снижается из-за кристаллического превращения алюмината кальция при средних температурах. Очевидно, что введенный CaO реагирует с SiO₂ и Al₂O₂ в бетоне с образованием некоторых легкоплавких веществ, что приводит к ухудшению высокотемпературных свойств материала.
При использовании технологии ультратонкого порошка, высокоэффективных добавок и научной градации частиц содержание цемента в бетоне снижается до менее 8%, а содержание воды снижается до ≤7%, и может быть приготовлен и введен в эксплуатацию низкоцементный ряд огнеупорных бетонов. Содержание CaO составляет ≤2,5%, а его эксплуатационные показатели в целом превосходят показатели огнеупорных бетонов на основе алюминатного цемента. Этот тип огнеупорных бетонов обладает хорошей тиксотропией, то есть смешанный материал имеет определенную форму и начинает течь при небольшом внешнем усилии. После снятия внешнего усилия он сохраняет полученную форму. Поэтому его также называют тиксотропным огнеупорным бетоном. Самотекучий огнеупорный бетон также называется тиксотропным огнеупорным бетоном. Относится к этой категории. Точное значение низкоцементных рядов огнеупорных бетонов до сих пор не определено. Американское общество по испытаниям и материалам (ASTM) определяет и классифицирует огнеупорные бетоны на основе содержания в них CaO.
Плотность и высокая прочность являются выдающимися характеристиками огнеупорных бетонов с низким содержанием цемента. Это хорошо для увеличения срока службы и эксплуатационных характеристик продукта, но также создает проблемы при обжиге перед использованием, то есть, если вы не будете осторожны во время обжига, может легко произойти заливка. Явление разрыва корпуса может, как минимум, потребовать повторной заливки, а в тяжелых случаях может поставить под угрозу личную безопасность окружающих рабочих. Поэтому в разных странах также проводились различные исследования обжига огнеупорных бетонов с низким содержанием цемента. Основные технические меры: разработка разумных кривых печи и введение отличных антивзрывных добавок и т. д., это может сделать огнеупорные бетоны. Вода удаляется плавно, не вызывая других побочных эффектов.
Технология сверхтонких порошков является ключевой технологией для огнеупорных бетонов с низким содержанием цемента (в настоящее время большинство сверхтонких порошков, используемых в керамике и огнеупорных материалах, имеют размер от 0,1 до 10 мкм и выполняют в основном функцию ускорителей дисперсии и структурных уплотнителей). Первая технология обеспечивает высокую дисперсность частиц цемента без флокуляции, а вторая обеспечивает полное заполнение микропор в теле заливки и повышает прочность).
В настоящее время широко используются такие типы ультрадисперсных порошков, как SiO2, α-Al2O3, Cr2O3 и т. д. Удельная площадь поверхности микропорошка SiO2 составляет около 20 м2/г, а размер его частиц составляет около 1/100 размера частиц цемента, поэтому он обладает хорошими заполняющими свойствами. Кроме того, микропорошки SiO2, Al2O3, Cr2O3 и т. д. также могут образовывать коллоидные частицы в воде. При наличии диспергатора на поверхности частиц образуется перекрывающийся двойной электрический слой, создающий электростатическое отталкивание, которое преодолевает силы Ван-дер-Ваальса между частицами и снижает энергию интерфейса. Это предотвращает адсорбцию и флокуляцию между частицами; в то же время диспергатор адсорбируется вокруг частиц, образуя слой растворителя, что также увеличивает текучесть бетона. Это также один из механизмов действия ультрадисперсного порошка, то есть добавление ультрадисперсного порошка и соответствующих диспергаторов может снизить расход воды в огнеупорных бетонах и улучшить текучесть.
Схватывание и твердение огнеупорных бетонов с низким содержанием цемента является результатом совместного действия гидратационной связи и когезионного связывания. Гидратация и твердение цемента из алюмината кальция в основном являются гидратацией гидравлических фаз CA и CA2 и процессом роста кристаллов их гидратов, то есть они реагируют с водой с образованием гексагональных чешуек или игольчатых CAH10, C2AH8 и Продукты гидратации, такие как кубические кристаллы C3AH6 и гели Al2O3аq, затем образуют взаимосвязанную конденсационно-кристаллизационную сетчатую структуру во время процессов отверждения и нагревания. Агломерация и связывание происходят из-за того, что активный ультрадисперсный порошок SiO2 образует коллоидные частицы при встрече с водой и ионами, медленно диссоциирующими из добавленной добавки (т. е. электролита). Поскольку поверхностные заряды двух частиц противоположны, то есть коллоидная поверхность адсорбирует противоионы, что приводит к уменьшению потенциала и конденсации при достижении адсорбцией «изоэлектрической точки». Другими словами, когда электростатическое отталкивание на поверхности коллоидных частиц меньше притяжения, возникает когезионное связывание под действием сил Ван-дер-Ваальса. После конденсации огнеупорного бетона, смешанного с кремнеземистым порошком, группы Si-OH, образовавшиеся на поверхности SiO₂, высушиваются и дегидратируются, образуя силоксановую сетчатую структуру (Si-O-Si), тем самым затвердевая. В силоксановой сетчатой структуре связи между кремнием и кислородом не ослабевают с повышением температуры, поэтому прочность также продолжает расти. В то же время, при высоких температурах сетчатая структура SiO₂ реагирует с заключенным в ней Al₂O₂, образуя муллит, что может повысить прочность при средних и высоких температурах.
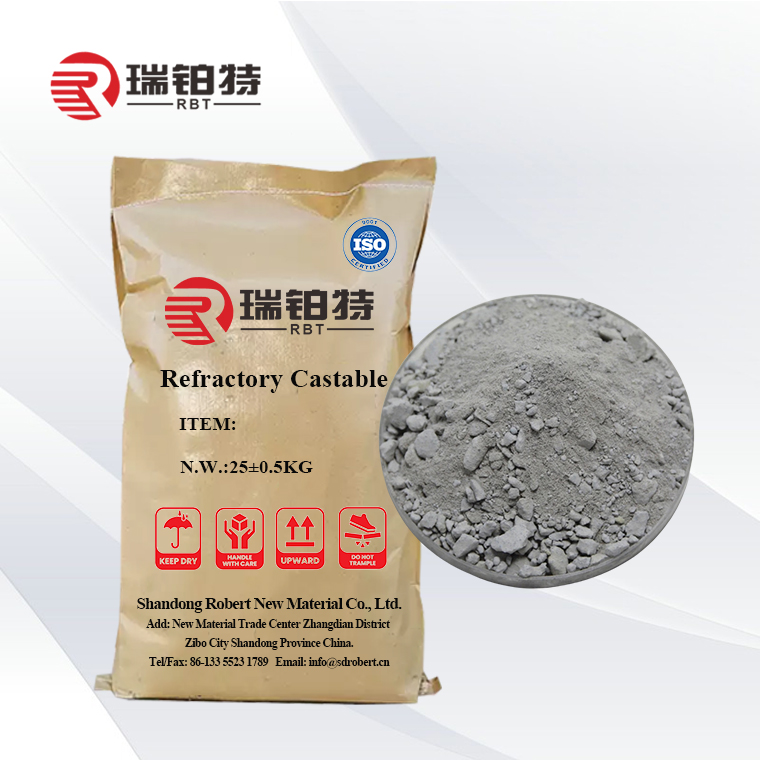
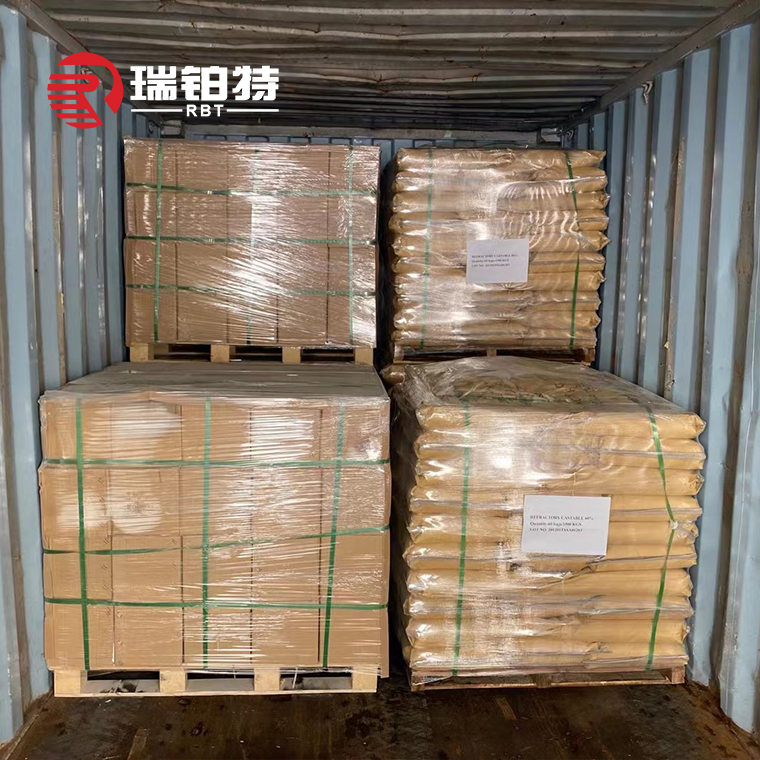
Время публикации: 28 февраля 2024 г.